Polished Concrete
The Toughest Concrete Solutions in Ontario!Polished concrete is concrete that has been treated with a chemical densifier and ground with progressively finer grinding tools.
The grinding tools are usually progressive grits of diamond grinding cup wheels and diamond polishing pads.[1] Typically, concrete is not considered polished before 400 grit, and it is normally finished to either the 800, 1500, or 3000 grit level. Stains and dyes are often applied to enhance polished concrete as well as other options such as scoring, creating radial lines, grids, bands, borders, and other designs.
Benefits
Polished concrete is considered a good sustainable design flooring option because it makes use of the materials already present. Most modern buildings are built on a concrete slab; polishing the exposed concrete eliminates the energy and material consumed by applying a floor covering. It is something to consider when building or modernizing towards a more green solution.
Polished concrete floors are low-maintenance, as they are more durable and easier to clean than many flooring options. Its relatively high coefficient of friction can make it non-slippery. Polished concrete reduces dust mite and allergen problems, and does not support mould growth. Anecdotal evidence suggests highly reflective polished concrete reduces lighting needs and improves natural lighting, but as yet there has not been a study to confirm this. Polished concrete flooring is hard wearing and will not chip or dent like softer surfaces such as timber. Mopping with warm soapy water once a week is the only maintenance required. A concrete floor that has been hardened and polished will have an extremely long life expectancy compared to other flooring. For example, tile that may only last 10–20 years(tile is a vague term. porcelain will last hundreds of years with no maintenance), but a polished concrete floor that has been properly maintained may give 100+ years of service.
LEED 2009 standards contain guidelines for using polished concrete flooring to qualify for LEED credits.
New or retrofit
In simple terms, the process of polishing concrete is similar to sanding wood. Heavy-duty polishing machines, for example concrete grinder, are used to gradually grind down surfaces to the desired degree of shine and smoothness. The closest equivalent example would be polished granite or marble.
Polished concrete floor installation is categorised into two types: new floors, and retrofit floors.
New floors
New polished concrete slab
New floors require less work resulting in lower costs, but there are a few things to be aware of before a new concrete floor can be polished. Firstly the slab can contain a decorative aggregate. The three most common aggregates are river stone, granite, and black basalt mix, however the aggregate can be almost anything. The finished surface of the concrete will need to be finished to a high standard to facilitate the polishing process. During the finishing phase any decorative aggregates such as seashells, glass chips or even metal car parts can be dropped into the surface of the concrete. Builder needs to be aware as early as possible if the concrete is to be polished so that the final finish is of the best quality.
Retrofit floors
Retrofit floors can be done in two ways. The existing floor slab can be cut or sanded and the natural aggregate will be the feature or a topping slab with a minimum thickness of 50 mm can be added on top of the existing slab.
Diamond-polished concrete process
A diamond polished concrete floor is very time-consuming if done correctly, this is due to the fact that there are at least 10 to 15 steps involved. The general rule is to start the initial grinding with a coarse 16- or 30-grit diamond and finish with a 1500- or 3000-grit diamond, depending on the gloss level required. These diamonds are impregnated inside a metal- or resin-bonded segment. Typically the diamonds’ grit size will double once the first grind has been carried out. The use of 16- or 30-grit size diamonds, then use 60/80-grit diamonds followed by the 120-grit metal bond segments. The polishing process begins with a 50-grit diamond resin pad instead of a metal segment. When using the resin pads the steps may be 100, then 200, 400, 800, 1500 and finally 3000 grit. Throughout the process a densifier is used to harden the concrete surface, which allows the concrete to be polished. A number of densifiers can be used; these consist of a lithium, potassium sodium silicates. A grouting chemical is also used throughout the process to fill in any holes, cracks or imperfections that were exposed from the initial coarse grinding step.[2] The concrete is then sealed with a natural-look impregnating sealer; this sealer penetrates 2–5 mm inside the pores of the concrete preventing any deep staining from oils and spills.
Polished concrete is considered a good sustainable design flooring option because it makes use of the materials already present. Most modern buildings are built on a concrete slab; polishing the exposed concrete eliminates the energy and material consumed by applying a floor covering. It is something to consider when building or modernizing towards a more green solution.
Polished concrete floors are low-maintenance, as they are more durable and easier to clean than many flooring options. Its relatively high coefficient of friction can make it non-slippery. Polished concrete reduces dust mite and allergen problems, and does not support mould growth. Anecdotal evidence suggests highly reflective polished concrete reduces lighting needs and improves natural lighting, but as yet there has not been a study to confirm this. Polished concrete flooring is hard wearing and will not chip or dent like softer surfaces such as timber. Mopping with warm soapy water once a week is the only maintenance required. A concrete floor that has been hardened and polished will have an extremely long life expectancy compared to other flooring. For example, tile that may only last 10–20 years(tile is a vague term. porcelain will last hundreds of years with no maintenance), but a polished concrete floor that has been properly maintained may give 100+ years of service.
LEED 2009 standards contain guidelines for using polished concrete flooring to qualify for LEED credits.
New or retrofit
In simple terms, the process of polishing concrete is similar to sanding wood. Heavy-duty polishing machines, for example concrete grinder, are used to gradually grind down surfaces to the desired degree of shine and smoothness. The closest equivalent example would be polished granite or marble.
Polished concrete floor installation is categorised into two types: new floors, and retrofit floors.
New floors
New polished concrete slabNew floors require less work resulting in lower costs, but there are a few things to be aware of before a new concrete floor can be polished. Firstly the slab can contain a decorative aggregate. The three most common aggregates are river stone, granite, and black basalt mix, however the aggregate can be almost anything. The finished surface of the concrete will need to be finished to a high standard to facilitate the polishing process. During the finishing phase any decorative aggregates such as seashells, glass chips or even metal car parts can be dropped into the surface of the concrete. Builder needs to be aware as early as possible if the concrete is to be polished so that the final finish is of the best quality.
Retrofit floors
Retrofit floors can be done in two ways. The existing floor slab can be cut or sanded and the natural aggregate will be the feature or a topping slab with a minimum thickness of 50 mm can be added on top of the existing slab.
Diamond-polished concrete process[edit]A diamond polished concrete floor is very time-consuming if done correctly, this is due to the fact that there are at least 10 to 15 steps involved. The general rule is to start the initial grinding with a coarse 16- or 30-grit diamond and finish with a 1500- or 3000-grit diamond, depending on the gloss level required. These diamonds are impregnated inside a metal- or resin-bonded segment. Typically the diamonds’ grit size will double once the first grind has been carried out. The use of 16- or 30-grit size diamonds, then use 60/80-grit diamonds followed by the 120-grit metal bond segments. The polishing process begins with a 50-grit diamond resin pad instead of a metal segment. When using the resin pads the steps may be 100, then 200, 400, 800, 1500 and finally 3000 grit. Throughout the process a densifier is used to harden the concrete surface, which allows the concrete to be polished. A number of densifiers can be used; these consist of a lithium, potassium sodium silicates. A grouting chemical is also used throughout the process to fill in any holes, cracks or imperfections that were exposed from the initial coarse grinding step.[2] The concrete is then sealed with a natural-look impregnating sealer; this sealer penetrates 2–5 mm inside the pores of the concrete preventing any deep staining from oils and spills.
Grind-and-seal polished concrete process
This system is the standard polished concrete system where the concrete surface is ground to the desired level using coarse 16- or 30-grit metal-bonded diamonds. When the desired grind level is achieved, the surface is re-ground with usually a 60-grit diamond to remove any visible scratching. Grouting and patching may be required to fill any voids, holes, cracks or imperfections. The surface is then cleaned and prepared for the application of either a gloss or matte surface coating, or an impregnating enhancing sealer.
Process
New polished concrete floorProcess involved in polishing concrete:
1.The concrete floor is cut with a variety of diamond abrasive grits, usually, 3-8 depending on the gloss level desired. Many in the industry do not consider a 3-step grinding to be truly polished concrete. The 3-step process is often referred to as a hybrid polished concrete. This polishing can be done wet or dry depending on the site situation. Benefits of dry grinding include dust-free operation and easier clean-up since no slurry is created during the process. However dry grinding can expose workers as well as the HVAC system to harmful amorphous silica dust. Wet grinding eliminates this problem and has become increasingly popular because of this; however, the disposal of the slurry created also causes some concerns. Some companies have adopted strict silicosis policies due to the silica exposure of dry grinding. 2.A densifier is applied once the concrete is opened up and in a condition to readily accept the chemical. The step at which the densifier is applied is determined by the person polishing the concrete. A high-solids lithium silicate is used on many polished concrete floors. Sodium silicate and potassium silicates are also used. 3.The densifier is allowed to dry and cure for the manufacturers recommended time, followed by one or more abrasive cuts, which will polish the floor to the desired gloss. 4.Timing of delivery depends on the type of equipment that a contractor uses. It can be expected that a 32-inch grinder will average 600 square feet per hour per grit, and a large, Bobcat-mounted 3-headed grinder can grind 2,000 square feet per hour per grit. The Bobcat grinders have limited availability on the east and west coasts of the U.S. Some industry experts do not consider Bobcat grinders or remotely controlled grinders suitable for highly refined work.
Grind-and-seal polished concrete process
This system is the standard polished concrete system where the concrete surface is ground to the desired level using coarse 16- or 30-grit metal-bonded diamonds. When the desired grind level is achieved, the surface is re-ground with usually a 60-grit diamond to remove any visible scratching. Grouting and patching may be required to fill any voids, holes, cracks or imperfections. The surface is then cleaned and prepared for the application of either a gloss or matte surface coating, or an impregnating enhancing sealer.
Process
New polished concrete floor
Process involved in polishing concrete:
1. The concrete floor is cut with a variety of diamond abrasive grits, usually, 3-8 depending on the gloss level desired. Many in the industry do not consider a 3-step grinding to be truly polished concrete. The 3-step process is often referred to as a hybrid polished concrete. This polishing can be done wet or dry depending on the site situation. Benefits of dry grinding include dust-free operation and easier clean-up since no slurry is created during the process. However dry grinding can expose workers as well as the HVAC system to harmful amorphous silica dust. Wet grinding eliminates this problem and has become increasingly popular because of this; however, the disposal of the slurry created also causes some concerns. Some companies have adopted strict silicosis policies due to the silica exposure of dry grinding.
2. A densifier is applied once the concrete is opened up and in a condition to readily accept the chemical. The step at which the densifier is applied is determined by the person polishing the concrete. A high-solids lithium silicate is used on many polished concrete floors. Sodium silicate and potassium silicates are also used.
3. The densifier is allowed to dry and cure for the manufacturers recommended time, followed by one or more abrasive cuts, which will polish the floor to the desired gloss.
4. Timing of delivery depends on the type of equipment that a contractor uses. It can be expected that a 32-inch grinder will average 600 square feet per hour per grit, and a large, Bobcat-mounted 3-headed grinder can grind 2,000 square feet per hour per grit. The Bobcat grinders have limited availability on the east and west coasts of the U.S. Some industry experts do not consider Bobcat grinders or remotely controlled grinders suitable for highly refined work.
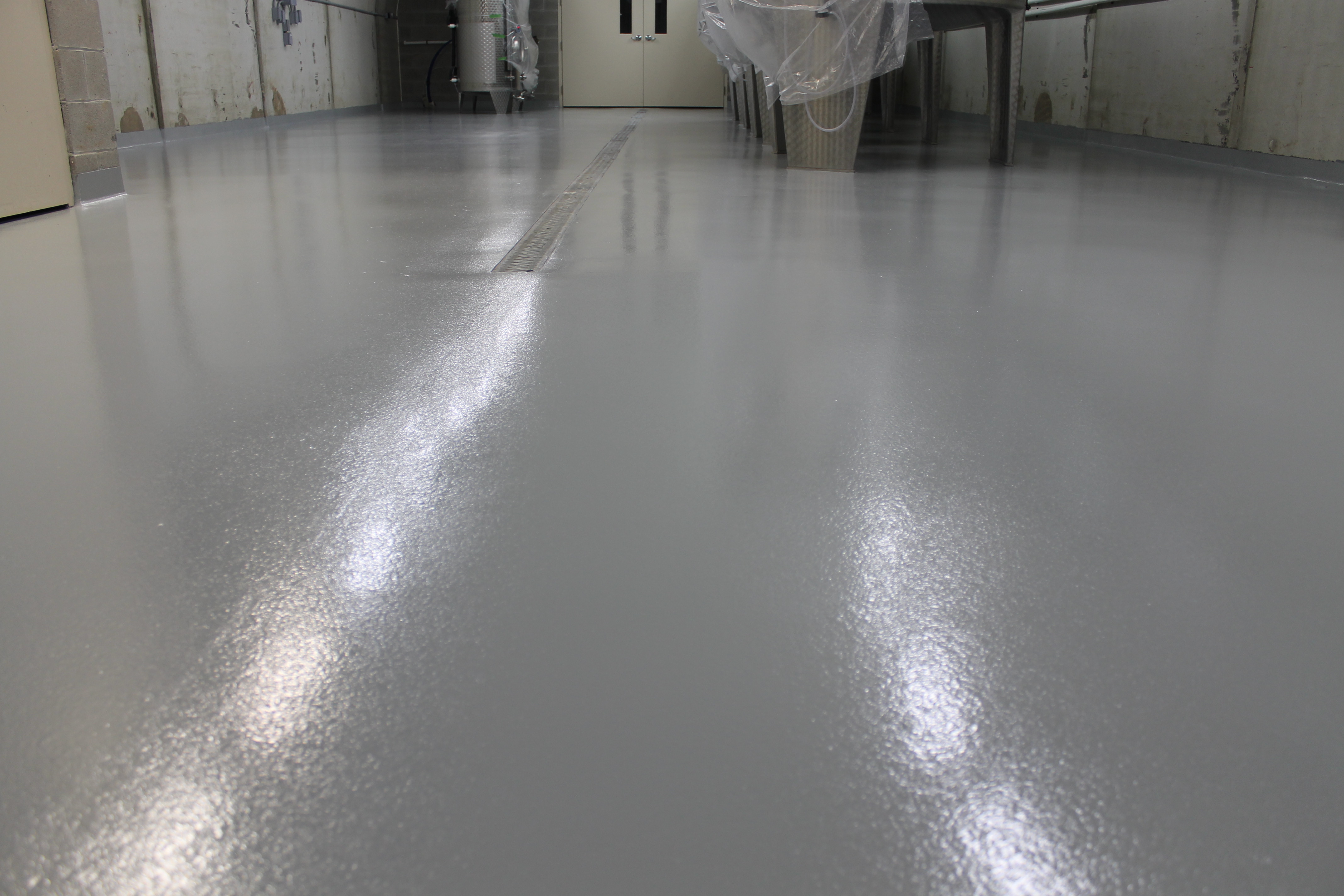
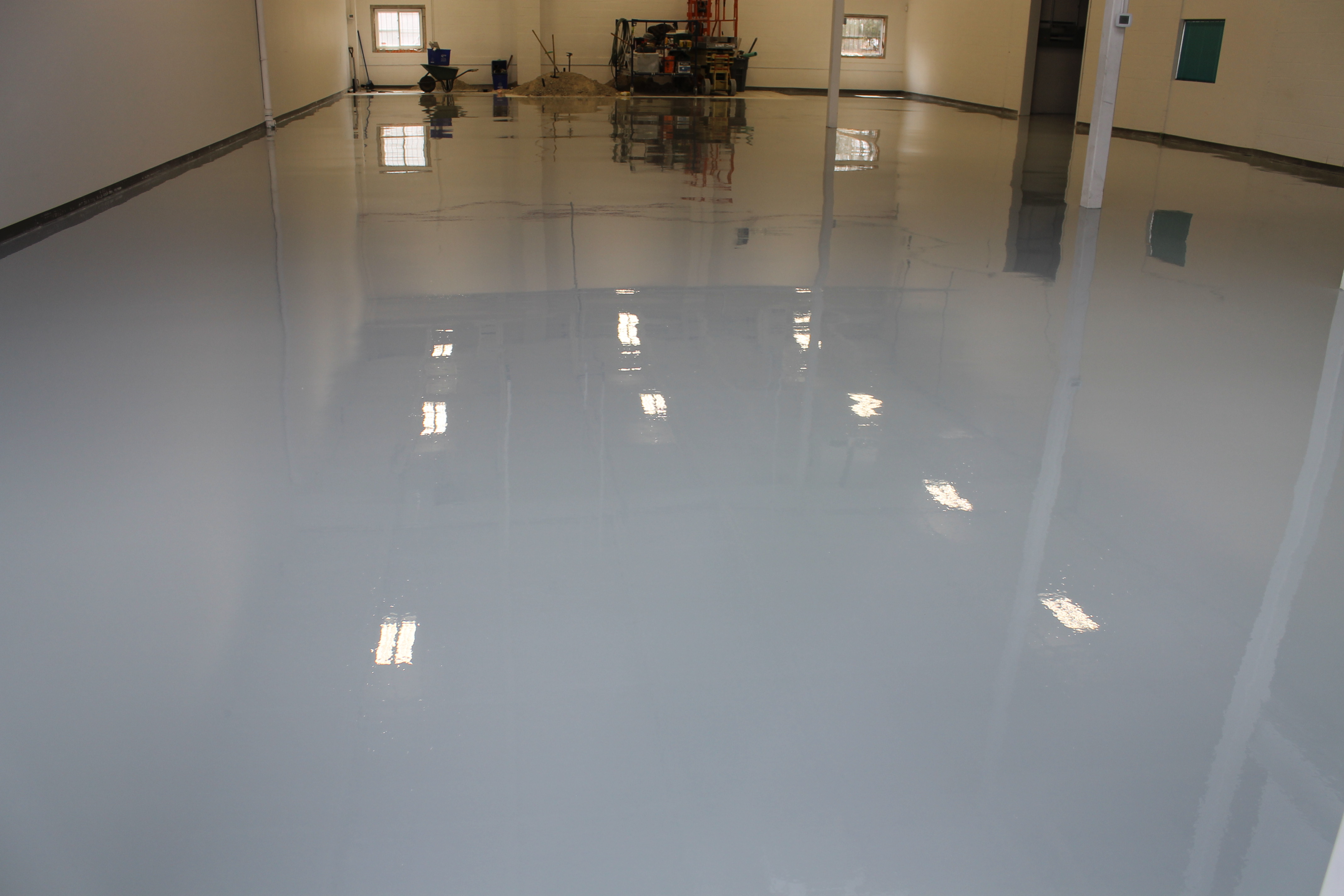

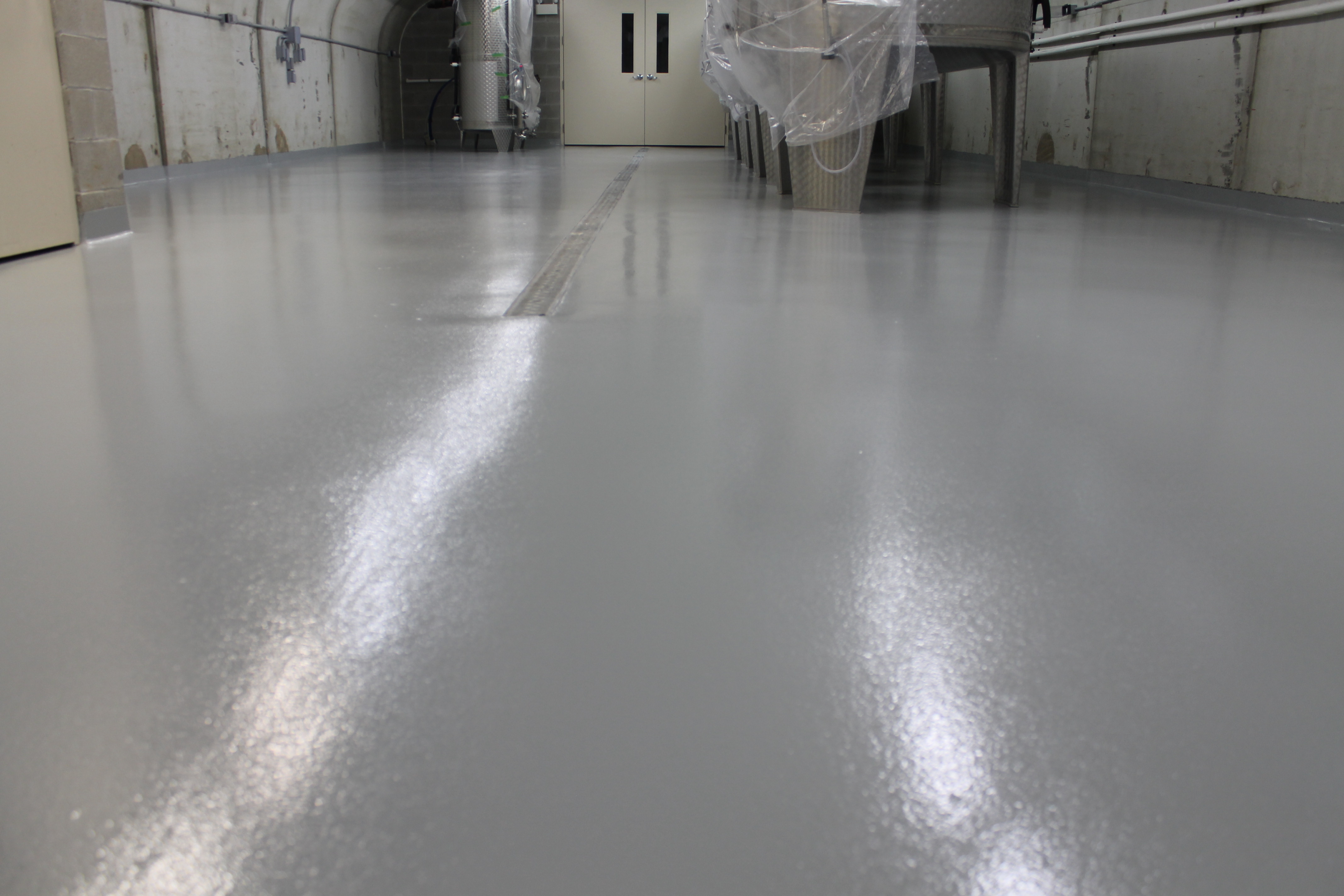
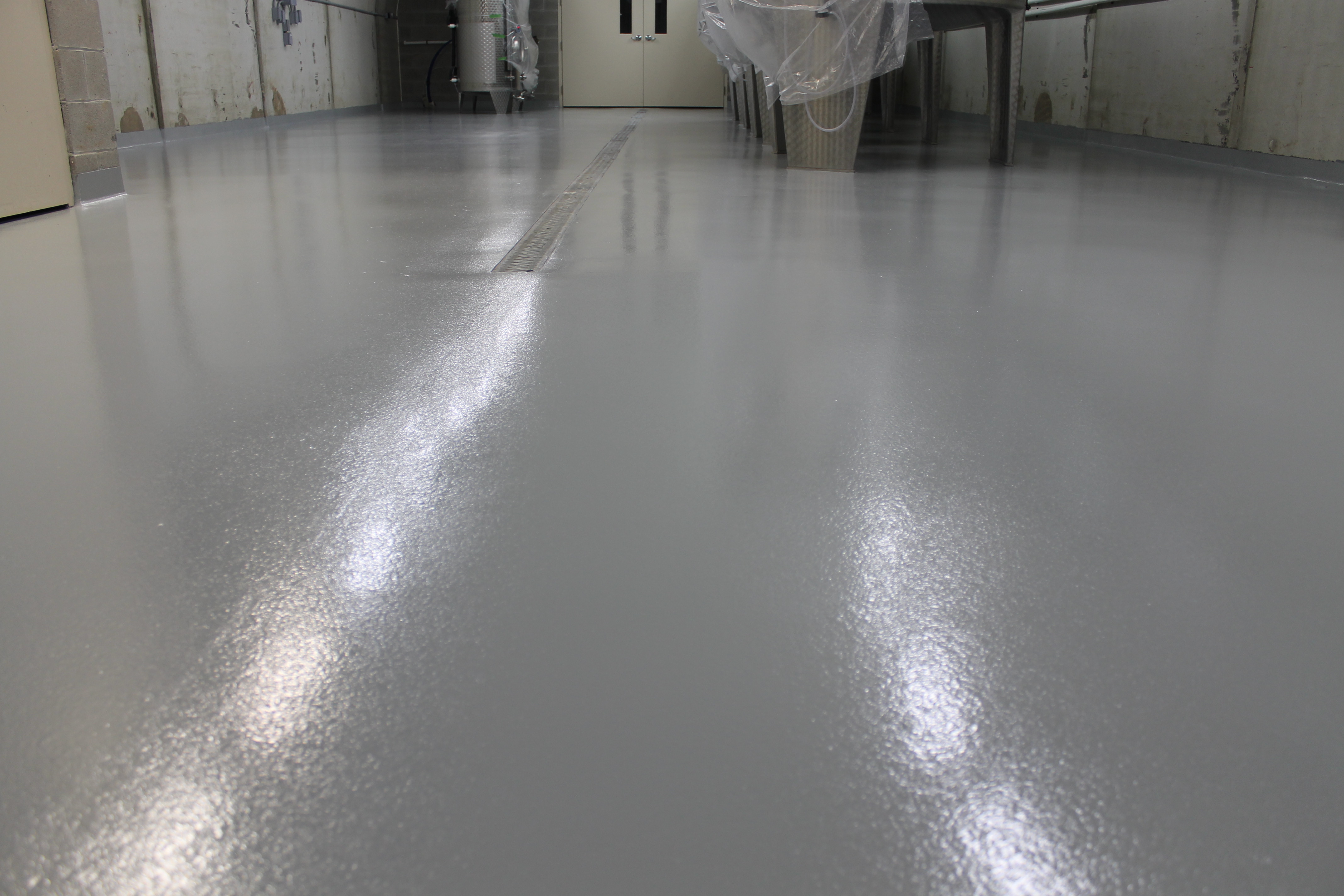
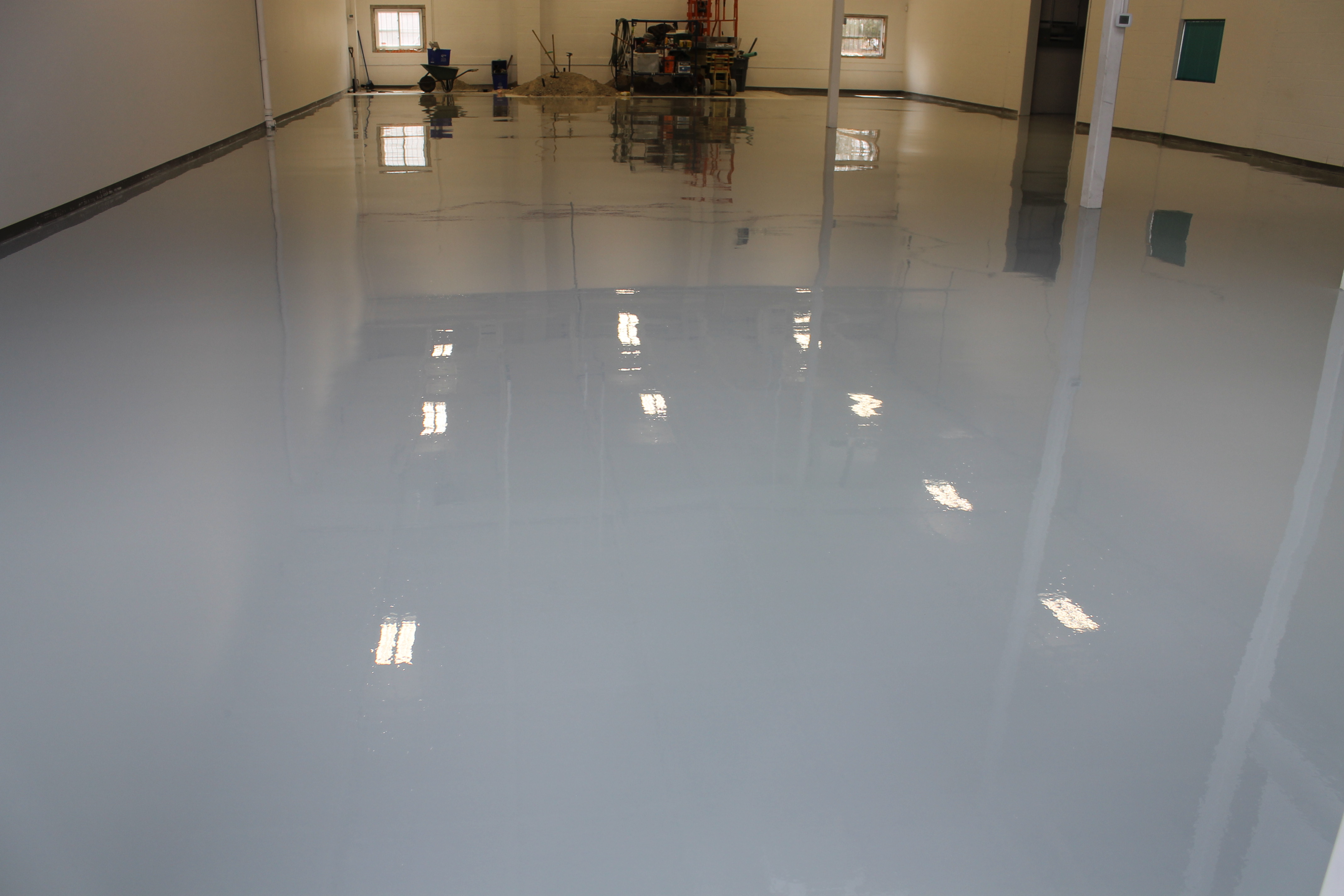

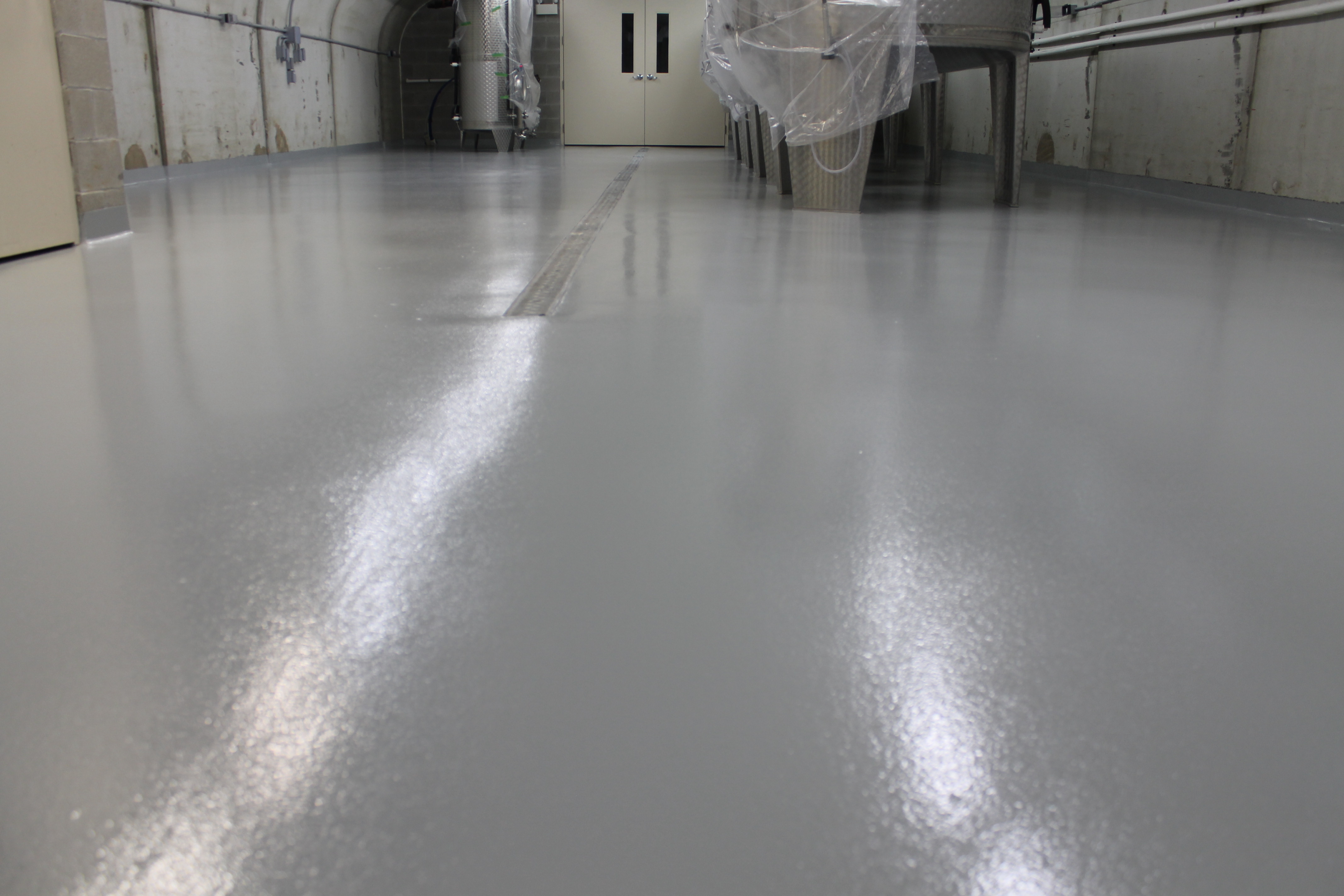
Find Out More
Contact us right now to get a free quote for your next residential or commercial project.